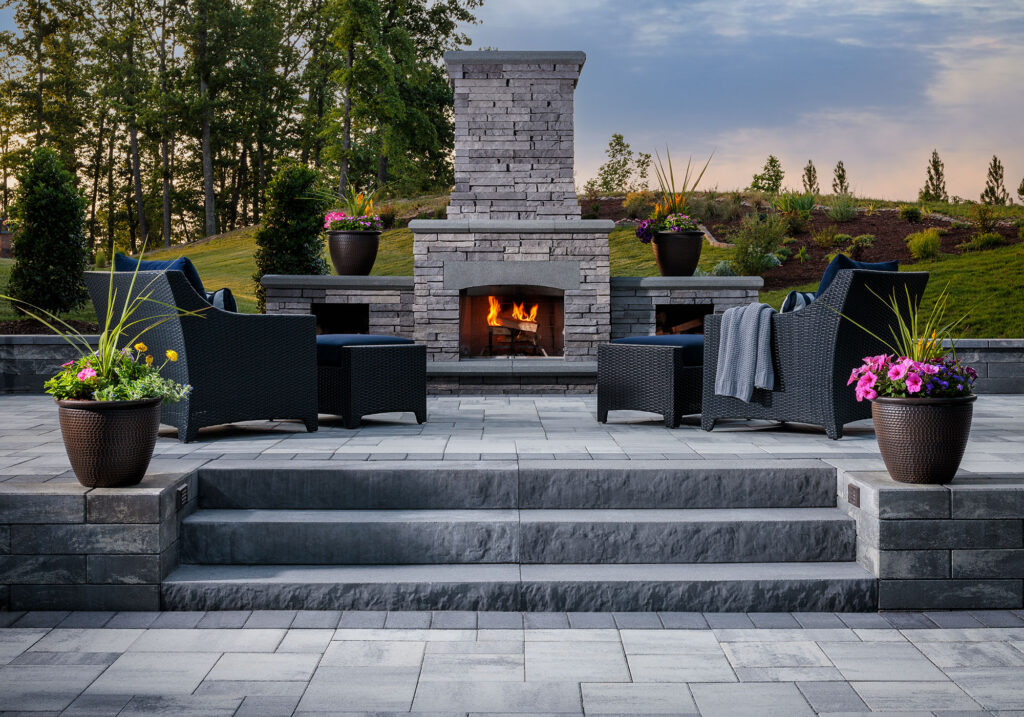
It's Good Business to Add Hardscapes & Natural Stone to Your Service Lineup.
As the demand for complete outdoor living spaces continues to grow, many landscapers and builders are finding new revenue opportunities by expanding into hardscaping and natural stone installation. If your business currently focuses on traditional residential or commercial landscaping, integrating hardscape services could open the door to higher-margin projects, increased customer satisfaction, and a stronger competitive edge.
The Market Is Growing – And So Are the Margins
Outdoor living isn’t just a trend—it’s a booming industry. Homeowners are investing in patios, walkways, retaining walls, outdoor kitchens, and fire features that blend design with functionality. According to industry research:
- The U.S. landscaping industry is valued at over $100 billion, and hardscaping is a key contributor to that figure.
- Hardscape projects often yield profit margins of 15–40%, significantly higher than typical soft scaping work (Gitnux, Horizon).
- Outdoor features like patios, decks, and stone walkways can recover 50–75% of their cost in home resale value.
Why Contractors Are Expanding Into Hardscaping
Here are a few reasons why forward-thinking builders and landscapers are integrating hardscaping into their services:
- Higher Project Value: A typical hardscape job commands more dollars than maintenance or planting work, boosting average project size and bottom-line performance.
- Increased Client Demand: Homeowners, multi-family residences, hotel and other businesses now expect the inclusion of outdoor spaces. Offering complete design-build services makes you more attractive to clients.
- Cross-Selling Opportunities: Existing clients are more likely to invest in hardscape features when bundled with landscape design or home builds.
- Year-Round Work Potential: In many climates, hardscaping can be performed outside traditional growing seasons, helping to extend your working calendar.
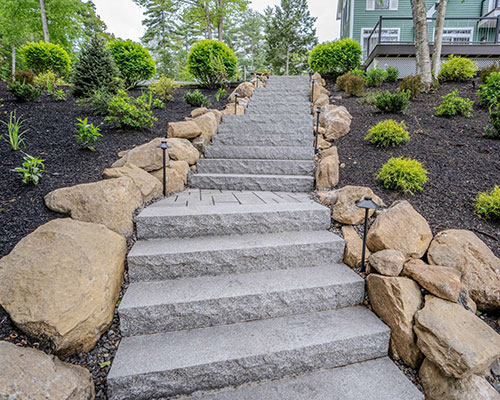
Natural Stone: A Smart Addition
Natural stone is one of the most sought-after materials in hardscaping, prized for its durability, elegance, and versatility. From flagstone patios and granite steps to stone veneers and boulder walls, stone adds both function and high-end appeal to residential and commercial properties.
Benefits of working with natural stone include:
- High perceived value among homeowners
- Long-lasting, low-maintenance performance
- Aesthetic flexibility to suit traditional, rustic, or modern designs
- Increased project prestige, setting you apart from competitors using only manufactured materials
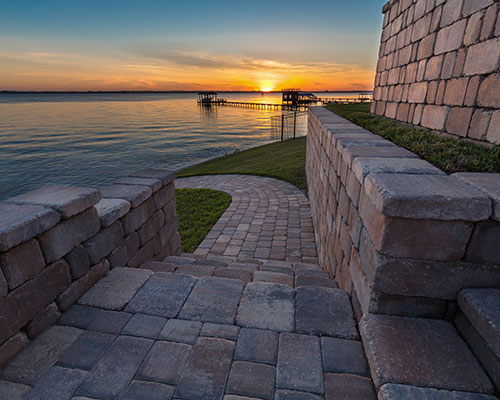
Manufactured Segmental Retaining Walls (SRWs) and Pavers
SRWs and pavers are essential building blocks for durable, visually appealing outdoor spaces. These versatile products offer both structural integrity and design flexibility, making them ideal for everything from functional retaining walls to stunning patios and walkways.
- Durability – Made from high-quality concrete or composite materials, ensuring long-term structural integrity
- Consistent Quality – Uniform size and strength make installation easier and reliable.
- Design Versatility – Available in various styles, colors, and textures for aesthetic appeal.
- Easy Installation – Modular systems often feature interlocking designs for quicker builds.
- Eco-Friendly – SRWs deliver erosion control while permeable pavers support drainage and control runoff.
Getting Started
Adding hardscaping or stone installation services doesn’t require a complete overhaul of your business. Many successful contractors start by:
- Training their crews in basic installation techniques (suppliers, vendors and industry associations provide educational opportunities)
- Partnering with experienced subcontractors while building in-house capabilities
- Sourcing high-quality materials from knowledgeable local suppliers
- Adding design and quoting tools to streamline client communication
It’s also important to build a reliable network of trusted suppliers and consultants who can provide the right materials, guidance, and technical support as you grow.
Whether you’re a landscaper looking to expand your design capabilities or a builder aiming to deliver turnkey outdoor environments, hardscaping is a strategic move that can pay dividends for years to come. At Outdoor Living Supply, we’re here to help you succeed—with expert guidance, high-quality materials, and the support you need to grow your business. Find an OLS location near you and take the next step in building beautiful, profitable outdoor spaces.