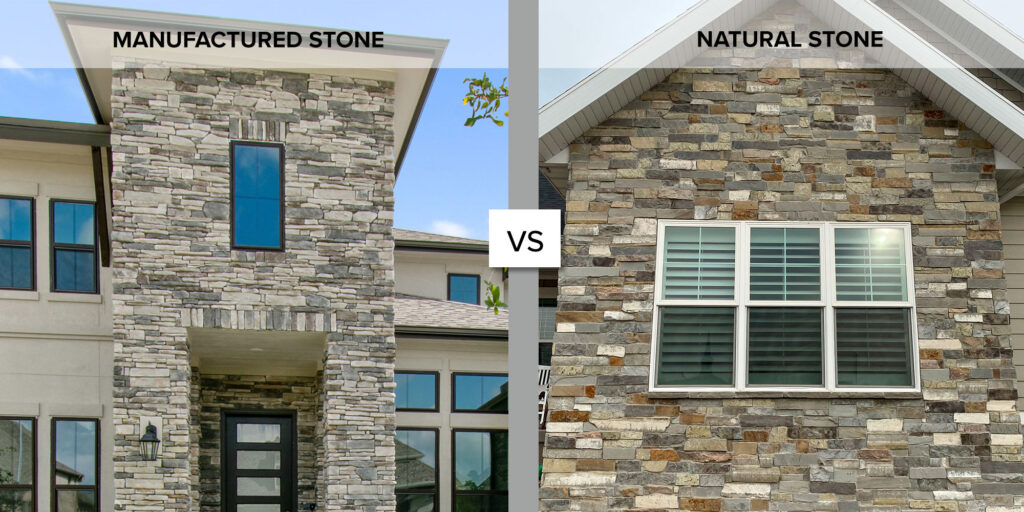
Manufactured Stone vs. Natural Stone
Find the Right Product for Exterior Home Projects.
As a contractor, selecting the right materials for exterior home projects is essential for delivering quality results while balancing cost, durability, and client satisfaction. Manufactured stone and natural stone are the two prevailing choices for homeowners to make a statement with their exteriors, each with its own advantages and disadvantages.
Manufactured Stone
Pros:
- Cost Efficiency: Manufactured stone is typically less expensive than natural stone, which can help you offer competitive pricing and attract budget conscious clients.
- Design Versatility: With a wide array of colors, textures, and styles, manufactured stone allows you to meet diverse client preferences and customize projects to exact specifications.
- Ease of Installation: Its lighter weight reduces labor costs and simplifies the installation process, allowing for quicker project turnaround times.
- Consistent Quality: The uniformity in color and shape ensures predictable results and reduces waste, enhancing project efficiency.
Cons:
- Durability Concerns: While durable, manufactured stone may not match the longevity of natural stone, potentially leading to future maintenance issues and impacting client satisfaction.
- Perceived Value: Some clients may prefer the unique look and feel of natural stone, viewing manufactured options as less prestigious.
- Environmental Impact: The production process involves chemicals and energy, which may be a concern for environmentally conscious clients.
Natural Stone
Pros:
- Premium Aesthetic: Natural stone’s distinctive and timeless beauty can significantly enhance a project’s appeal, attracting higher-end clientele willing to invest in quality.
- Exceptional Durability: Its ability to withstand harsh weather conditions makes it a long-lasting choice, reducing the likelihood of future callbacks and maintenance.
- Eco-Friendly Option: Locally sourced and sustainably quarried natural stone can appeal to clients who prioritize environmental responsibility.
- Value Addition: The use of natural stone can increase property value, making it an attractive option for clients looking to enhance their investment.
Cons:
- Higher Costs: Natural stone generally comes with higher material and installation costs, which can be a barrier for some clients.
- Labor Intensive: Its heavier weight can lead to increased transportation and labor costs, potentially extending project timelines.
- Limited Customization: Natural stone offers fewer color and texture options compared to manufactured stone, which might limit design flexibility.
- Maintenance Needs: Regular sealing and maintenance may be required to preserve its appearance and durability, which could be a concern for clients.
For contractors, both manufactured stone and natural stone present viable options for exterior home projects, each with distinct business implications. Manufactured stone offers cost efficiency, design versatility, and ease of installation, making it ideal for budget-conscious projects and quick turnarounds. On the other hand, natural stone provides unmatched aesthetic appeal, durability, and eco-friendliness, appealing to a high-end clientele seeking long-term value.
When advising your clients it’s important to consider their budget, design preferences, and maintenance expectations. By understanding the pros and cons of each material, you can tailor your recommendations to meet client needs and optimize your project outcomes.